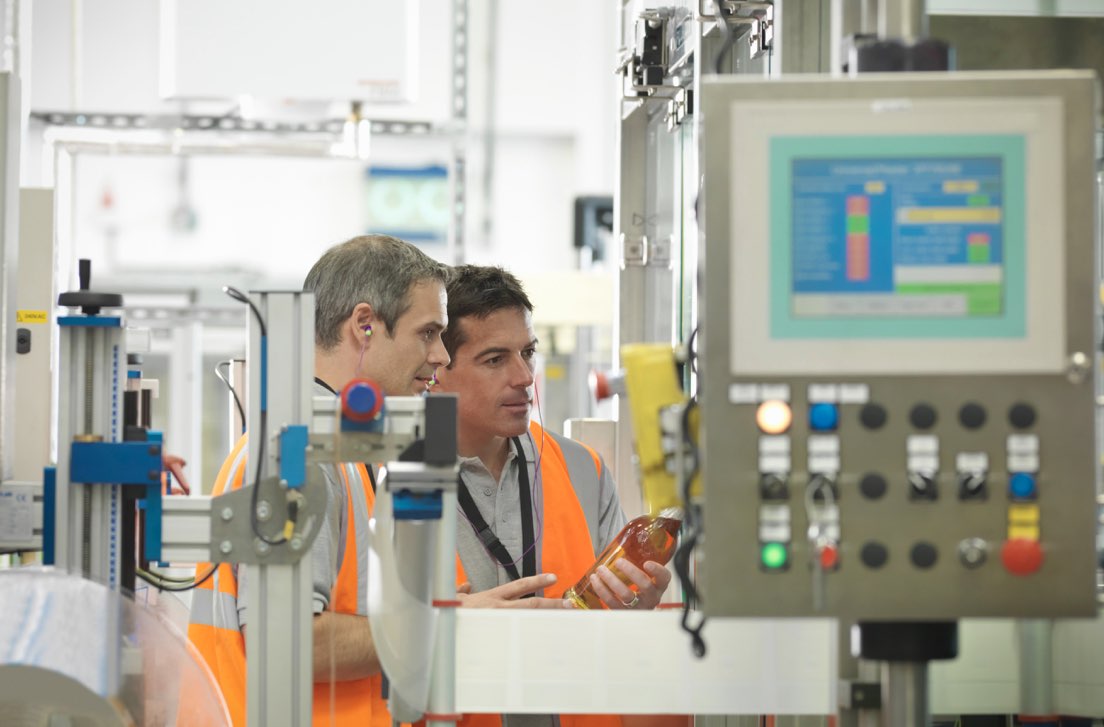
Abbiamo già avuto modo di parlare di risk and safety management, una serie di processi che supportano decisioni scientifiche e pratiche all'interno della gestione della sicurezza degli impianti. Anche se l'uso delle pratiche di risk and safety management non si sostituisce all'obbligo delle industrie di rispettare i requisiti normativi, un'efficace gestione del rischio può facilitare decisioni migliori e più rapide all'interno del processo produttivo, e può fornire alle autorità di regolamentazione una maggiore garanzia delle capacità di una società di far fronte a potenziali rischi.
Influendo sull'entità e sul livello della supervisione regolamentare diretta, in questo articolo riprendiamo, a puro scopo illustrativo e non esaustivo, alcune aree di utilizzo degli strumenti principali per la gestione del rischio collegato alla qualità e sicurezza dei prodotti, così come elencate al documento in lingua inglese EudraLex - Volume 4 - Good Manufacturing Practice (GMP) - Parte III. Buona lettura.
La FMEA fornisce una valutazione dei potenziali guasti all'interno dei processi e il loro probabile effetto sui risultati e sulle prestazioni del prodotto. Una volta stabiliti i potenziali guasti, la riduzione del rischio può essere utilizzata per eliminarli, contenerli, ridurli o controllarli.
Potenziali aree di utilizzo
La FMEA può essere utilizzata per dare priorità ai rischi e monitorare l'efficacia delle attività di controllo. Questa procedura può essere applicata ad attrezzature e strutture, e può essere utilizzata per analizzare operazioni di fabbricazione e il loro effetto su prodotti o processi. La FMEA identifica elementi ed operazioni all'interno del sistema che lo rendono vulnerabile. I risultati possono essere utilizzati come base per l'ulteriore analisi dei rischi, o per guidare l'implementazione delle risorse.
La procedura FMEA può essere estesa, per incorporare un'indagine sul grado di rilevabilità, diventando quindi una Failure Mode Effect e Critically Analysis (FMECA). Affinché tale analisi possa essere eseguita, è necessario stabilire le specifiche del prodotto o del processo. Con la FMECA si possono identificare i luoghi in cui potrebbero essere necessarie azioni preventive per ridurre al minimo i rischi.
Potenziali aree di utilizzo
L'applicazione FMECA, soprattutto nell'industria farmaceutica, è utilizzata principalmente per guasti e rischi associati ai processi di fabbricazione; tuttavia, non si limita a questa applicazione. I risultati di una FMECA rappresentano un "punteggio" di rischio relativo a ciascun potenziale guasto, che viene utilizzato per stilare una classifica di priorità.
L'FTA è un approccio al risk management che presuppone il fallimento della funzionalità di un prodotto o di un processo. Questo strumento valuta i guasti del sistema (o sottosistema) uno alla volta, ma può combinare più cause di fallimento, identificando le catene causali. I risultati sono rappresentati graficamente sotto forma di un diagramma ad albero. A ciascun livello dell'albero, le combinazioni delle modalità di errore sono descritte con operatori logici (AND, OR, ecc.). L'FTA si basa sulla comprensione del processo da parte degli esperti, per identificare i fattori causali.
Potenziali aree di utilizzo
L'FTA può essere utilizzato per stabilire il percorso verso la causa principale dell'errore, per indagare sui reclami al fine di comprendere appieno la causa principale e garantire che i miglioramenti previsti risolvano completamente il problema e non conducano ad altri problemi (ad esempio, risolvono un problema, ma causano un problema diverso). L'FTA, quindi, è utile sia per la valutazione del rischio che per lo sviluppo di programmi di monitoraggio.
L'HACCP può essere utilizzato per identificare e gestire i rischi associati a pericoli fisici, chimici e biologici (inclusa la contaminazione microbiologica). L'HACCP è molto utile quando la comprensione del prodotto e del processo è sufficientemente completa da supportare l'identificazione dei punti critici di controllo. L'output di un'analisi HACCP è un'informazione sulla gestione del rischio che facilita il monitoraggio di punti critici non solo nel processo di produzione, ma anche in altre fasi del ciclo di vita.
L’HAZOP si basa su una teoria che presuppone che gli eventi di rischio siano causati da deviazioni dal progetto o dalle intenzioni operative. È una tecnica di brainstorming sistematica per identificare i pericoli usando le cosiddette "parole guida” (ad esempio “no, altro, parte di” e così via). Queste parole-guida vengono applicate a parametri pertinenti (ad esempio, contaminazione, temperatura) per aiutare a identificare potenziali deviazioni dalle intenzioni di progettazione.
Potenziali aree di utilizzo
L’HAZOP può essere applicato ai processi di produzione, compreso l’outsourcing, nonché ai fornitori a monte, alle attrezzature e alle strutture per sostanze farmaceutiche. Nell'industria farmaceutica è usato soprattutto per valutare i rischi per la sicurezza del processo. Come nel caso dell'HACCP, l'output di un'analisi HAZOP è un elenco di operazioni fondamentali per la gestione del rischio. Ciò facilita il monitoraggio regolare dei punti critici nel processo di produzione.
Il PHA è uno strumento di analisi basato sull'applicazione di precedenti esperienze o conoscenze di un pericolo o guasto, per identificare rischi futuri, situazioni pericolose ed eventi che potrebbero causare danni, nonché per stimare la probabilità di accadimento per una data attività, struttura, prodotto o sistema.
Potenziali aree di utilizzo
Il PHA è utile quando si analizzano i sistemi esistenti, o si stabiliscono le priorità dei pericoli, laddove le circostanze impediscono l'utilizzo di una tecnica più ampia. Può essere utilizzato per la progettazione di prodotti, processi e strutture, nonché per valutare i tipi di rischi per ciascun prodotto generico, quindi per la classe del prodotto e infine per il prodotto specifico. Il PHA è più comunemente usato all'inizio dello sviluppo di un progetto, quando ci sono poche informazioni sui dettagli di progettazione e sulle procedure operative. Per questo, il PHA è spesso il precursore di ulteriori studi.
In conclusione, il risk and safety management è fondamentale per garantire la qualità dei prodotti offerti dalle aziende e un elevato grado di sicurezza degli stessi.
A livello pratico, gli strumenti sopra elencati forniscono le basi per una metodologia di gestione del rischio.
Tuttavia, ci sono alcune componenti strumentali, all’interno dei processi produttivi, che possono favorire le pratiche di risk management. Ad esempio, per tutti i processi che comprendono la misurazione di temperatura, è importante che essa sia sempre precisa e che gli strumenti non manifestino delle non conformità.
Digitalizzazione e Plant Asset Management diventano quindi elementi fondamentali per avere sotto controllo tutti gli strumenti del proprio impianto.
Se vuoi approfondire, puoi cliccare sul bottone qui sotto e leggere i casi studio di successo in relazione alla sicurezza e disponibilità degli impianti chimici!
Benvenuti sul portale digitale di Endress+Hauser: uno spazio in cui raccontiamo casi di studio, soluzioni, servizi e prodotti su misura per tutti i settori industriali. Ogni giorno potrete accedere a informazioni specifiche in merito a misure di livello radar, misure di analisi, soluzioni energy, servizi di taratura e approfondimenti dal mondo dell'automazione di processo.
Endress+Hauser Italia S.p.A
Una Società del Gruppo Endress+Hauser AG
Via Fratelli Di Dio, 7 20063 Cernusco s/N MI
Codice Fiscale e Partita IVA 01942780154
Tel. +39 02 92 192 1
Fax. +39 02 92 107 153
E-mail tiziana.perchiazzi@endress.com
Copyright © 2025 Endress+Hauser Management AG - Partita IVA 01942780154
Dati societari | Privacy Policy | Cookies | Condizioni di utilizzo