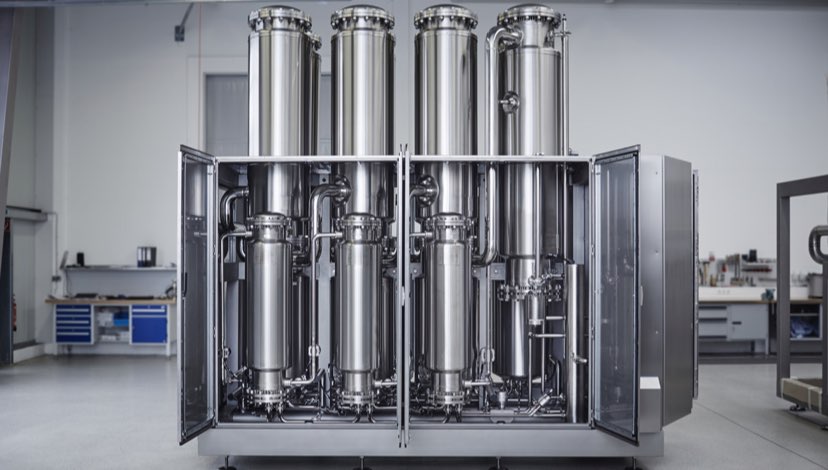
La produzione di acqua per iniettabili (WFI - Water For Injection) è un processo dell’industria farmaceutica - e più in generale delle life sciences - che implica un uso consistente di energia. L’efficienza energetica riveste pertanto un ruolo sempre più critico. Ma non solo: le norme qualitative sempre più stringenti rendono importante un approccio di “Quality by Design” nel processo produttivo. In questo caso studio analizzeremo la soluzione offerta da Endress+Hauser che ha permesso al cliente di ottenere un risparmio sui costi energetici di produzione di acqua per iniettabili.
Ti interessano i casi di successo dei clienti che hanno scelto l'approccio Quality by Design di Endress+Hauser? Clicca in basso e scarica i casi studio!
Indice:
- Produzione acqua per iniettabili: lo stato dell’arte
- Efficienza energetica nella distillazione
- Efficienza energetica: i misuratori di Endress+Hauser
- Risparmio energetico e innovativo recupero del calore
- Il risvolto pratico del concetto di “Quality by Design”
In Europa, fino al 2016 l'acqua per iniettabili nel campo farmaceutico doveva essere prodotta tramite una fase finale di distillazione. Questo era quanto stabilito dalla farmacopea europea. Secondo altre farmacopee internazionali, invece, la distillazione era una delle possibili fasi per la produzione di acqua per iniettabili. Nella distillazione, l’acqua precedentemente purificata (PW, Purified Water) viene fatta evaporare in grandi colonne e quindi nuovamente condensata. In questo processo termico, il vapore industriale viene utilizzato come vettore energetico, che viene convogliato in un sistema separato per il riscaldamento dell’acqua precedentemente purificata.
Per un impianto di Springe, in Germania, il cliente ha messo a punto una soluzione di depurazione dell’acqua, composta da un impianto per la purificazione preliminare e la successiva distillazione per la produzione di acqua per iniettabili.
La sfida era riuscire a produrre, a seconda delle prestazioni, grandi quantità di acqua per iniettabili (fino a 6 m3/h), in quanto necessari per i processi di lavaggio nella lavorazione del plasma sanguigno. La distillazione richiede un grande quantitativo di energia. Rimaneva quindi aperta una questione: quale rendimento si genera nella produzione per acqua per iniettabili? La risposta arriva dal bilanciamento dei flussi di energia con i misuratori di Endress+Hauser.
Il vapore industriale messo a disposizione dal gestore per il riscaldamento delle colonne viene registrato da un misuratore di portata a vortice di tipo Prowirl F 200, di Endress+Hauser. In questo contesto vengono misurati anche pressione e temperatura per la compensazione. Il controllo dell’acqua precedentemente purificata proveniente dall’impianto “PW” e lo scarto viene eseguito con un misuratore di portata Coriolis di tipo Promass P 100. Grazie alle differenze tra i due flussi di massa, l’acqua per iniettabili prodotta può essere calcolata con estrema precisione.
Liquiphant FTL33 come interruttore di livello min di una colonna
I processi termici negli impianti che producono acqua per iniettabili generano grandi quantità di calore residuo, che normalmente non vengono utilizzate: di solito è addirittura necessario il raffreddamento aggiuntivo degli ambienti di produzione. Inoltre, il calore generato dalle colonne e dalle tubazioni nell’impianto rappresenta un grande rischio durante il funzionamento, perché può causare ustioni al personale. Ma la situazione è cambiata: il cliente ha sviluppato un sistema per il recupero del calore nell’impianto. Nell’innovativa soluzione, le colonne di distillazione sono rivestite da porte in acciaio inox. Solo la parte superiore delle colonne sporge dall’impianto chiuso verso l’alto. Lo spazio interno viene raffreddato in modo mirato a 35-45° C tramite scarichi dell’aria integrati nella struttura dello skid. La temperatura di questo spazio interno viene misurata continuamente. In questo modo, il calore residuo non viene disperso nell'ambiente di produzione, ma può essere utilizzato in maniera mirata, ad esempio, come calore per il riscaldamento di altre aree produttive. Non è quindi più necessario raffreddare ulteriormente l’ambiente di produzione, risparmiando energia e riducendo i costi.
Il raffreddamento dello spazio interno dell’impianto determina una maggiore durata dei sistemi di misurazione e regolazione, la cui elettronica non funziona in modo affidabile con temperature a lungo al di sopra degli 80° C.
L’impianto di distillazione composto da otto colonne offre possibilità ottimali di recupero del calore. Il rendimento dell’impianto dipende inoltre dalla purezza dell'acqua messa a disposizione e da buone soluzioni di degassificazione. Dal 100% di acqua di alimentazione convogliata vengono generati il 98% di prodotto e appena il 2% di acqua di scarico.
La produzione dell'impianto di distillazione può essere regolata tra 1 e 6 m3/h tramite valvole di regolazione (a seconda delle necessità). Tutto questo è possibile grazie alle misurazioni altamente precise con un elevato turn-down; l’efficienza energetica è così costantemente elevata.
Il responsabile del settore life sciences di Endress+Hauser con un responsabile d'impianto del cliente.
In conclusione, il caso studio mostra come una tecnologia innovativa di misurazione della portata offre la possibilità di bilanciamento dei flussi di energia e del “monitoraggio in tempo reale” dell’efficienza dell’impianto.
Il rendimento energetico può essere definito tramite il rilevamento del rapporto tra energia termica del prodotto (acqua per iniettabili) ed energia termica del vettore energetico (vapore industriale). Nell’impianto descritto, il rendimento supera costantemente il 90%.
Vuoi avere informazioni più dettagliate su come migliorare l’efficienza energetica nel tuo impianto e raggiungere importanti vantaggi con il Quality by Design? Clicca sul bottone qui sotto e parla con un nostro esperto!
Benvenuti sul portale digitale di Endress+Hauser: uno spazio in cui raccontiamo casi di studio, soluzioni, servizi e prodotti su misura per tutti i settori industriali. Ogni giorno potrete accedere a informazioni specifiche in merito a misure di livello radar, misure di analisi, soluzioni energy, servizi di taratura e approfondimenti dal mondo dell'automazione di processo.
Endress+Hauser Italia S.p.A
Una Società del Gruppo Endress+Hauser AG
Via Fratelli Di Dio, 7 20063 Cernusco s/N MI
Codice Fiscale e Partita IVA 01942780154
Tel. +39 02 92 192 1
Fax. +39 02 92 107 153
E-mail tiziana.perchiazzi@endress.com
Copyright © 2025 Endress+Hauser Management AG - Partita IVA 01942780154
Dati societari | Privacy Policy | Cookies | Condizioni di utilizzo